We’ve all been there, work orders piling up and clients demanding outrageous requests and tight deadlines. It’s hard enough to make sure orders are completed with high quality, but how do you stay on top of them? What’s the easiest way to make sure orders get done in timely and orderly fashion? How do you manage changes to these orders? These are issues some of our clients in construction, manufacturing and machine shops deal with on a day to day basis.
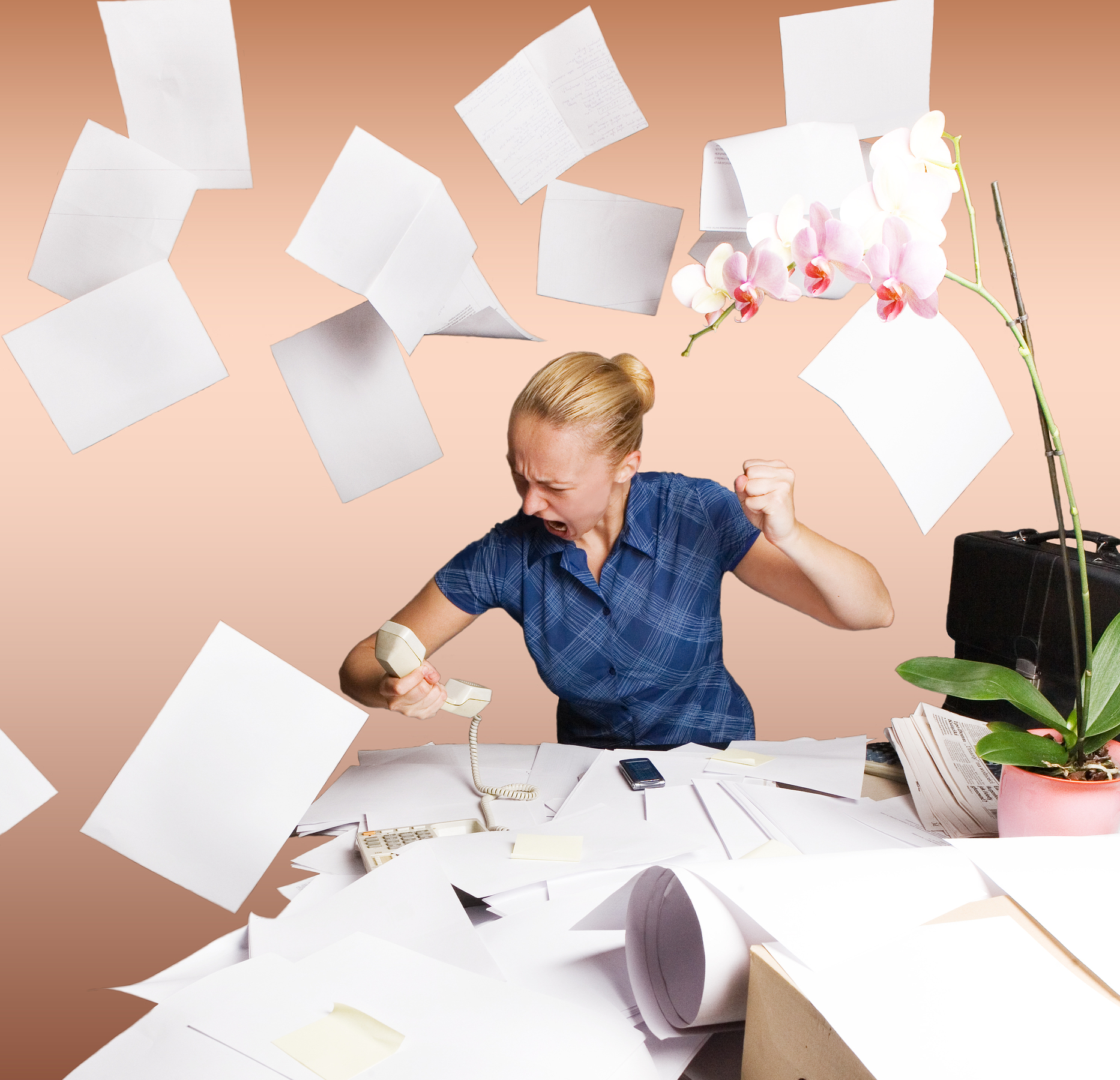
Well, there’s good news! Tracking work orders doesn’t have to be a daunting task. With the right system and tools, you can easily manage these helping your business run smoothly. In this blog post, I’ll list methods you can use to stay on top of your work orders.
1 - Stacked Trey
We believe in keeping things simple. So for smaller businesses, ones that don’t have many orders going at the same time, having a stacked trey with all your work orders might do the trick. I know this might sound obvious to some, but it’s amazing how we like to complicate things by adding fancy systems that are really not necessary. The stack trey works like a queue and you work on the next job up. You can move orders with higher priority up the list.
2 - White Board / Cork Board
An improvement of the trey box is having a white board or cork board, with the list of all the current work orders in process. This system allows your shop to easily visualize what’s going, what to work on next and the status of each thing. A white board can be set up with a job per row and each column can have its level of completion per stage. A priority and due date columns are usually handy to have.
3 - Spreadsheet
The digital version of the white board would be the MS Excel Spreadsheet. Work order tracking with a spreadsheet can be done easily. It is the same concept as the white board, except that it’s easier to maintain and more information can be added. It’s also easy to print and save various copies of it. Unlike the white board, Excel allows you to cut and paste rows, so you can change the priority of each order by moving rows around.
4 - Project Management System
This approach is a powerful way to track your work orders. A machine shop management software or small manufacturing software allows you to easily store detailed information about each order, customer and subcontractor. They can keep track of inventory and provide you with valuable insights into your business. These systems allow you to also share and edit data across your business which is important if you need to keep many people up to date with the latest changes. These systems can usually talk to your accounting system of choice such as QuickBooks, or Simply Accounting.
5 - Enterprise Resource Planning (ERP)
Depending on the size of your business, you might already have or might require a complete integrated solution. ERP systems allow for your accounting system and project management system to ‘live’ in one place and communicate with each other. These solutions usually involve higher costs but allow you to cut down on time by having all your information in one place. Although they are very popular, I’m not a fan of ERPs because in my own opinion they are usually very clunky, hard to use and expensive to customize.
There you have it. You are now ready to start thinking of how you can incorporate one of these options to better manage your work orders. When evaluating the solutions, be sure to keep in mind effort, to create and upkeep. To see results especially with the more thorough options, it means keeping them up to date which will involve putting in time that you may not have. Is there other ways to manage your work orders? How do you do it? What are some good practices for each? Let me know below.